Новые скорости. Hyundai Trans Kazakhstan выходит на полную мощность
Эксперты отмечают: пандемия притормозила автопром. Пит-стоп предприятий, нехватка комплектующих, проблемы с логистикой вызвали дефицит готовых машин, снизилась и динамика рынка в целом. Однако, несмотря на такую ситуацию, отечественному заводу Hyundai Trans Kazakhstan удалось продолжать работать без остановок.
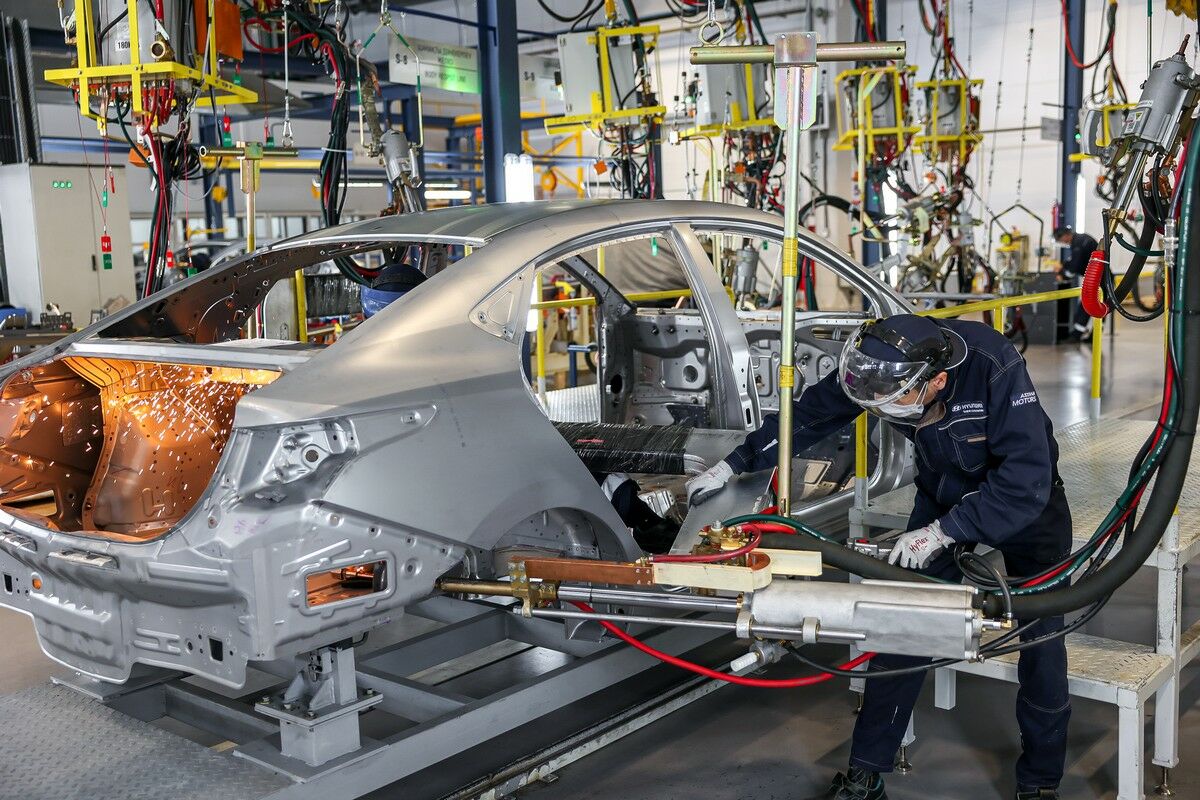
Еще и двух лет не прошло с момента запуска Hyundai Trans Kazakhstan, а предприятие уже выходит на проектную мощность, открывает новые экспортные страны, обкатывает и запускает технологию мелкоузловой сборки популярного кроссовера Hyundai Tucson. Как отечественному предприятию удается набирать такую скорость развития и что все-таки мешает на этом пути?
В 2021 году с конвейера Hyundai Trans Kazakhstan сошло 26 тысяч автомобилей. В 2022-м предприятие планирует выпустить уже 45 тысяч машин. То есть завод готов почти к двукратному росту объемов производства! Кстати, 30 процентов произведенных машин будут уезжать в Узбекистан, Кыргызстан, Беларусь. Более того, на Hyundai Trans Kazakhstan планируют развивать производство комплектующих для автомобилей и поставлять их на другие заводы.
- В этом году мы планируем собрать мелкоузловым способом порядка 10 тысяч автомобилей. 30 процентов из них - это Hyundai Accent, 70 процентов - Hyundai Tucson. В 2023 году мы планируем нарастить этот показатель до 15 000 машин, - увлеченно рассказывает журналистам генеральный директор “Астана Моторс” Бекнур НЕСИПБАЕВ.
Именно он проводит экскурсию по заводу в рамках медиатура для СМИ. Сразу делаем остановку на первом участке, он один из самых важных. Цех сварки. По бокам огромного зала уже стоит новое оборудование, которое позволит делать мелкоузловую сборку Hyundai Tucson. Уже через несколько дней технологи из Южной Кореи приступят к его установке на линии. А пока на площадке производят другую популярную модель - Hyundai Accent. Чтобы собрать из множества деталей готовый кузов, мастерам необходимо провести свыше тысячи операций. И это только в цехе сварки. Именно сюда подаются штампованные изделия. Боковина, крыша, задняя и передняя части привариваются к днищу. Затем авто получает свой VIN-код, на него крепят двери, капот, багажник. Интересно, что все эти этапы сварки знакомы каждому мастеру, ведь он успевает набить руку на всех участках.
- Нам в цехе сварки нужны универсальные сотрудники. Если у нас сотрудник проработал одну смену на посту сварки днища автомобиля, то на следующий день он работает на другом посту. Нам важно, чтобы сотрудник знал, как и что делается, - объясняет Бекнур Несипбаев.
После сварки кузов уходит в цех окраски, который больше похож на огромный SPA-комплекс для авто. Судите сами: здесь по периметру находятся 14 ванн.
В девяти из них происходят разные этапы очистки кузова, затем он погружается в катафорезную ванну, где наносится защитный слой от коррозии. После этого кузов авто поочередно помещают еще в четыре емкости, где происходит отмывка. Далее машина сушится в специальной печи и попадает в зону нанесения мастики. Затем уходит на грунтовку, где кузов готовят к покраске, нанесению базового слоя и лака. И только потом она доходит до цеха сборки.

В цехе сборки кузов становится полноценным авто. Мастера комплектуют салон, закладывают всю техническую начинку. Кстати, эту кропотливую работу на автозаводе делают… девушки. Да, на этом участке, как, впрочем, и на всем технологическом пути, я увидела множество мастериц.
- Этапы производства, которые касаются качества окраски, нанесения мастики, сборки деталей салона, чаще всего выполняют именно девушки. Эта работа требует большой концентрации и внимания. Девушки с этой задачей справляются лучше, чем мастера-мужчины, - подмечает Бекнур Несипбаев.
После сборки авто заправляют всеми техническими жидкостями и отправляют на пост контроля качества. Здесь тестируют геометрию колес, тормозную систему. Уже потом машину ждет тест-драйв. Кстати, проверку на качество продукция проходит не только на выходе, но и на каждом цикле производства. Причем в системе оценки качества исключен человеческий фактор.
Сотрудники контроля качества находятся в прямом подчинении директора завода. Это сделано специально, чтобы избежать конфликта интересов. Мастера, которые проводят контроль качества, имеют право остановить процесс, если контроль не пройден.
Прежде чем начать серийное производство тех же Hyundai Accent, наших мастеров обучали искусству мелкоузловой сборки южнокорейские инженеры Hyundai Motor Company. Шестимесячные тренировки на испытательных образцах позволили достигнуть необходимого промышленного качества на всех этапах производства. Осталось максимально повысить мобильность. Для примера: мощность цеха сварки - 3,5 авто в час. Специалисты этого участка довели объем пока до 2,5 машины. Конечно, есть куда двигаться дальше. Но уже сегодня мастера завода - высококлассные специалисты, каждый из них на вес золота. Текучка кадров исключена. Для этого здесь разработали свою систему мотивации сотрудников, а их сегодня около 700.
- Средняя зарплата сотрудников составляет 290 тысяч тенге. Питание на заводе бесплатное. Так как в наших цехах работают люди из пригорода Алматы, мы организовали доставку наших сотрудников до и после работы. И сейчас мы уже начали процесс проектирования общежития малосемейного типа для наших сотрудников. Первое общежитие начнем строить в конце 2022 года. Это 120 квартир малосемейного типа. На первом этаже мы сделаем детский садик. Все это будет предоставляться бесплатно, - уточнил Бекнур Несипбаев.
Предприятие также планирует готовить и новых специалистов. Уже сейчас завод приглашает лучших студентов нескольких технических вузов на оплачиваемую практику. В планах - взять шефство и над колледжами. Без подготовки специалистов расширяться заводу будет сложно. На рынке острый дефицит инженеров. И здесь это прочувствовали. Чтобы собрать команду, потребовалось целых полгода. И это не единственное препятствие, возникшее на пути Hyundai Trans Kazakhstan, который начал работать в пик мирового коронакризиса.
- Произошел мировой дефицит многих компонентов, тех же микросхем. Люди ушли на удаленку, и во всем мире возрос спрос на бытовую технику. Заводы, которые производят полупроводники, переквалифицировались и стали выпускать бытовую технику. Когда автомобильные заводы возобновили работу, то столкнулись с тем, что запасы микросхем истощились. Произошел коллапс, - констатирует Бекнур Несипбаев.
Проблемы возникли и в логистике. К примеру, контейнеры автозавода с комплектующими на полгода застряли в Китае. Предприятию пришлось оперативно менять схему транспортировки.
- Теперь комплекты из Южной Кореи мы получаем через Владивосток. Они идут примерно 40-45 дней, но зато мы уверены в том, что они точно придут. Конечно, через Китай логистика была дешевле. В феврале 2021 года мы за один контейнер платили 3500 долларов, а на днях контракт подписали по цене 11 700 долларов, - подсчитывает Бекнур Несипбаев.
Удорожание логистики, нехватка материалов, локдауны привели к тому, что мировой автопром существенно “съехал” вниз по объемам производства продукции и продажам.
- В той же Европе падение происходит на 5-7 процентов, в Китае тоже наблюдалось снижение. Если мы возьмем 2021 год, то Казахстан, несмотря на пандемию и ковидные ограничения, прирос в продажах на 26 процентов. Это автомобили, производимые не только в Казахстане, но и импортируемые в том числе. Российский рынок вырос на 6 процентов. То есть казахстанские игроки рынка справились с ситуацией гораздо лучше, - анализирует Бекнур Несипбаев.
Рост производства и продаж Hyundai Trans Kazakhstan связан с тем, что предприятие за два года ни разу не остановилось. Несмотря на мировой дефицит деталей авто, южнокорейский партнер постоянно отправлял комплектующие, постепенно увеличивая объемы. Ведь отечественный завод заслужил доверие южнокорейского партнера. Они смогли развить производство, освоить более технологичную мелкоузловую сборку. Увеличив ее содержание в общем объеме продукции, “Астана Моторс”, в состав которой входит Hyundai Trans Kazakhstan, планирует построить завод по выпуску компонентов для автомобилей.
- У нас есть планы по производству резиновых ковриков для машин. Это то, что можно сделать в ближайшее время. Планируем также освоить выпуск автомобильных сидений. У нас уже подписан меморандум о сотрудничестве с южнокорейской компанией Youngsan Glonet, которая является аккредитованным производителем компонентов и оборудования для заводов Hyundai. Мы начинаем работать и с другими казахстанскими предприятиями. Хотим помочь им пройти аккредитацию в Южной Корее у Hyundai, готовы поделиться своим опытом, - объясняет Бекнур Несипбаев.
Двойное увеличение производства, акцент на локализацию производства, создание новых рабочих мест и целого кластера предприятий вокруг Hyundai Trans Kazakhstan. Планы, конечно, серьезные. Возможности, желание, умение для их реализации есть. Но для того, чтобы отечественному автопрому загорелся зеленый свет, считает Бекнур Несипбаев, необходима защита рынка от автохлама:
- Какая-то защита нашего рынка от импорта авто нужна. Если убрать все защитные меры государства, компания “Астана Моторс” точно не обанкротится. Мы имеем 30-летний опыт импортерства, сможем быстро наладить поставки автомобилей из РФ, Южной Кореи, Арабских Эмиратов, США. Да и рабочее место в ритейле создать очень легко, и стоимость их создания относительно небольшая - 5-10 тыс. долларов. А на производстве создание рабочего места обходится от 100 до 150 тысяч. Но завтра что будет, когда мы слезем с нефтяной иглы? Как страна будет дальше развиваться? Мы за то, чтобы казахстанские производства развивались!
Елена БАХАРЕВА, Алматы